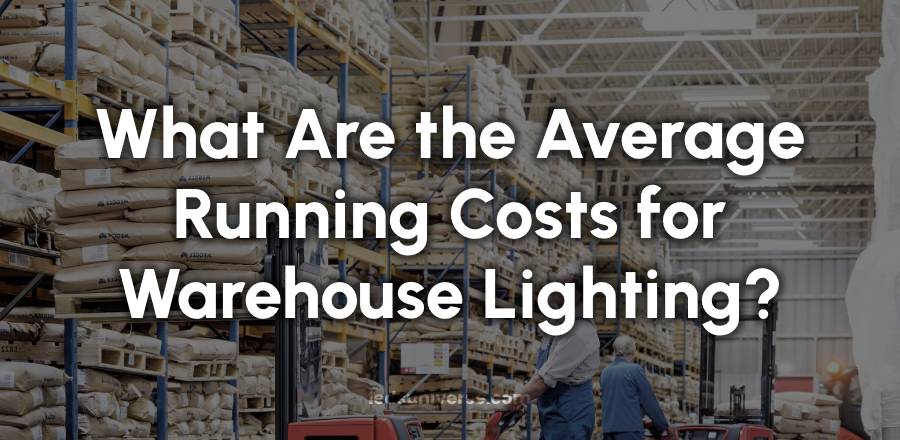
As the lights flicker on, so does a hidden cost—one that accumulates with every kilowatt-hour consumed, every bulb replaced, and every system maintained. Have you ever wondered how much your warehouse lighting is truly costing your business?
Warehouse operations often require substantial energy input, and lighting plays a major role in the overall operational cost. The need for effective and efficient lighting is evident in large spaces where safety, productivity, and energy efficiency intersect. Understanding the various components that contribute to lighting expenses in a warehouse environment is essential for managing costs effectively and identifying potential areas for improvement.
Reach out for free lighting consultation
Factor | Description | Impact on Costs |
---|---|---|
Energy Consumption | Different lighting types consume varying amounts of electricity. | Traditional fluorescent/HID lights: 50-100 watts; LEDs: 10-20 watts. |
Continuous operation (24/7) increases energy bills significantly. | Estimated increase of 20-30% in monthly energy costs for continuous use. | |
Poorly positioned lights may require more fixtures, leading to unnecessary energy use. | Potential for 15-25% higher energy costs due to over-lighting. | |
Hours of Operation | Longer usage results in higher energy consumption and increased wear on fixtures. | Increased operational costs of up to 40% for 24/7 operations vs. limited schedules. |
Frequent use shortens the lifespan of bulbs, leading to higher replacement costs. | Replacement costs can rise by 30-50% for high-use environments. | |
Lighting Design and Layout | Optimal design uses fewer fixtures for effective illumination, lowering installation costs. | Potential savings of 10-20% on initial setup costs with efficient design. |
Poorly planned layouts require more fixtures or higher-powered lights, increasing expenses. | Increased installation costs by 15-30% due to inefficient layout. | |
Efficient fixtures can reduce the overall number of lights needed, lowering long-term costs. | Long-term savings of 20-35% on energy and maintenance expenses. | |
Maintenance and Replacement | Traditional lights require more frequent replacements than LEDs, increasing maintenance costs. | Replacement costs for fluorescents/HID: $5-$15 per bulb; LEDs: $1-$5. |
Downtime for maintenance can lead to productivity losses. | Potential productivity loss cost: $100-$500 per hour depending on warehouse operations. | |
Proactive maintenance strategies can prevent costly emergency repairs. | Savings of 20-40% on maintenance costs through regular inspections. |
Table of Contents
ToggleThe type of lighting used within a warehouse significantly impacts overall energy consumption. Different types of lights consume varying amounts of electricity, which translates into diverse energy costs. Traditional lighting solutions, such as fluorescent or high-intensity discharge (HID) lights, tend to use more power compared to more modern and energy-efficient options like LED lights.
Energy consumption is measured in kilowatt-hours, and the longer the lights are in use, the more energy they consume. Warehouses operating 24 hours a day experience higher energy bills due to continuous use. However, the type of lighting can mitigate these costs. LED lights, for example, offer a higher level of energy efficiency, using a fraction of the energy required by traditional lighting solutions while providing the same or even better illumination.
Lighting layout also plays a role in energy consumption. Poorly positioned lights may require more fixtures to provide adequate illumination, leading to unnecessary energy usage. Additionally, the brightness level, or lumens, required for different tasks in a warehouse will affect energy consumption. Over-lighting certain areas can be as wasteful as under-lighting others, meaning that balancing illumination levels is key to controlling energy expenses.
The duration of lighting use within a warehouse has a direct effect on energy consumption and, subsequently, on lighting expenses. Warehouses that operate continuously will naturally see higher lighting expenses than those operating on a limited schedule. Depending on the specific nature of the business, some warehouses require constant lighting to ensure smooth operations and worker safety.
Operational hours also impact the rate at which lighting fixtures wear out. More frequent use translates into shorter lifespans for bulbs and fixtures, resulting in higher replacement costs and the need for more frequent maintenance. Therefore, operational hours not only affect energy costs but also increase the likelihood of having to replace lighting components more often, adding to overall lighting expenses.
For businesses looking to reduce lighting expenses, adjusting operational hours or incorporating automated systems that dim or turn off lights in unoccupied areas can help control energy usage without compromising safety or efficiency.
The design and layout of lighting systems in a warehouse directly influence both installation and operational costs. Warehouses with optimal lighting design use fewer fixtures to achieve effective illumination, reducing initial setup costs as well as ongoing energy consumption. On the other hand, poorly planned lighting layouts may require more fixtures or higher-powered lights, leading to increased installation and operational expenses.
A well-designed layout ensures that light is distributed evenly throughout the space, minimizing dark spots and shadows that could compromise worker safety or impede productivity. When lighting is arranged to optimize energy use, fewer lights can illuminate the entire space, keeping both energy and maintenance costs lower.
Lighting design also involves the choice of lighting fixtures themselves. Fixtures designed to reflect or distribute light more efficiently can help reduce the overall number of lights needed, which translates into lower energy and maintenance costs over time.
Maintenance is an ongoing expense for warehouse lighting, and the frequency of maintenance depends on the type of lighting used. Traditional lights, such as HID or fluorescent bulbs, have a shorter lifespan than LED lights, which means they need to be replaced more often. The cost of replacement bulbs, as well as the labor involved in replacing them, adds to the overall lighting expenses.
Additionally, lighting maintenance often requires shutting down operations in certain areas of the warehouse, leading to downtime and potential productivity losses. This downtime can be minimized with longer-lasting lighting solutions, such as LEDs, which require less frequent maintenance and have longer operational lifespans.
The initial cost of lighting systems may be high for energy-efficient solutions, but over time, the lower maintenance and replacement costs can offset this investment. A proactive approach to lighting maintenance, such as scheduling regular inspections and repairs, can help prevent more expensive emergency repairs or replacements, further reducing overall costs.
Upgrading to energy-efficient lighting systems, particularly LED lights, can result in significant long-term savings. Although the initial investment for LEDs may be higher compared to traditional lights, the savings on energy consumption and maintenance costs make it a worthwhile investment over time.
LED lights consume less electricity and have a much longer lifespan than fluorescent or HID bulbs. This means that while the upfront cost of installing LEDs might be higher, the energy savings and reduced maintenance needs can lead to lower overall expenses. Additionally, LEDs produce less heat, reducing the need for additional cooling in the warehouse, further contributing to cost savings.
Making the switch to energy-efficient lighting is not just about replacing bulbs but also about optimizing the overall lighting system. Installing dimmers, motion sensors, or automated controls can help ensure that lights are only in use when needed, further reducing energy waste.
Smart lighting systems are an increasingly popular option for warehouses looking to reduce lighting expenses. These systems allow for the automation of lighting based on occupancy, time of day, or specific tasks being performed. By ensuring that lights are only in use when necessary, smart lighting systems can help significantly reduce energy consumption and lower operating costs.
Motion sensors are particularly useful in warehouses where certain areas are not constantly in use. When installed in less frequently accessed spaces, these sensors can automatically turn off or dim lights when the area is unoccupied, saving energy without compromising safety. Smart lighting systems can also adjust brightness levels based on natural light availability, further reducing energy consumption.
Automated controls also offer the ability to monitor and adjust lighting remotely, providing warehouse managers with greater control over their energy use. By using data to analyze patterns in lighting usage, managers can make informed decisions about how to optimize lighting systems for maximum efficiency and cost savings.
Natural light can be an effective way to reduce lighting expenses, particularly in warehouses with large skylights or windows. By allowing daylight to illuminate the warehouse during working hours, businesses can reduce their reliance on artificial lighting, leading to lower energy consumption.
Maximizing the use of natural light requires careful planning of warehouse layout and operations. Skylights and windows need to be positioned in a way that maximizes sunlight while minimizing glare or overheating. Additionally, some warehouses may need to consider shading or other controls to prevent excessive heat from entering the building, which could offset any savings in lighting costs by increasing cooling expenses.
Incorporating natural light into the overall lighting strategy can help reduce energy costs, but it is important to ensure that safety and productivity are not compromised. Combining natural light with energy-efficient lighting solutions can create a balanced and cost-effective lighting system that meets the needs of the warehouse.
Keeping a warehouse’s lighting system well-maintained is another way to control expenses. Regular maintenance, such as cleaning fixtures and replacing worn-out components, can help ensure that the lighting system operates at peak efficiency.
Proactive repairs and maintenance help prevent the need for more costly emergency repairs or replacements. For example, a flickering light might seem like a minor issue, but if left unaddressed, it could lead to more significant problems with the electrical system. By addressing small issues early on, businesses can avoid the higher costs associated with major repairs.
Scheduled maintenance checks can also help identify areas where the lighting system could be improved or upgraded. For example, replacing older fixtures with newer, more energy-efficient models can result in long-term savings. Regular maintenance can also extend the lifespan of lighting fixtures, reducing the frequency of replacements and lowering overall maintenance costs.
Many governments and regulatory bodies have implemented energy efficiency standards for commercial buildings, including warehouses. These standards often require businesses to use lighting systems that meet specific energy efficiency criteria, which can influence the choice of lighting solutions.
By complying with energy efficiency regulations, warehouses can avoid fines or penalties while also benefiting from lower energy costs. In some cases, compliance with these standards may also qualify businesses for rebates or incentives from utility companies or government programs.
Regulations regarding energy efficiency can vary by region, so it is important for warehouse operators to stay informed about the specific requirements in their area. Investing in energy-efficient lighting solutions not only helps reduce costs but also ensures that the warehouse remains compliant with all relevant regulations.
Warehouse lighting systems can have a significant impact on the environment, particularly in terms of energy consumption and carbon emissions. Traditional lighting solutions, such as fluorescent or HID lights, consume more energy and produce more emissions than energy-efficient alternatives like LEDs.
Reducing energy consumption through efficient lighting systems can help lower the warehouse’s carbon footprint, contributing to broader environmental sustainability efforts. Additionally, many energy-efficient lighting solutions are made from materials that are easier to recycle or dispose of safely, further reducing their environmental impact.
For businesses with sustainability goals, investing in energy-efficient lighting can be a way to demonstrate their commitment to reducing their environmental impact. This can also have benefits in terms of public perception, as more consumers and business partners seek to work with companies that prioritize sustainability.
Many utility companies and government programs offer incentives or rebates for businesses that upgrade to energy-efficient lighting systems. These programs are designed to encourage businesses to reduce their energy consumption by offering financial assistance for the initial cost of upgrading their lighting systems.
Rebates and incentives can help offset the upfront cost of installing energy-efficient lighting, making it more affordable for businesses to make the switch. Additionally, these programs may offer ongoing incentives for maintaining energy-efficient practices, further reducing overall lighting expenses.
Businesses looking to take advantage of these incentives should research the programs available in their area and ensure that their lighting upgrades meet the specific requirements for eligibility. By participating in these programs, businesses can reduce the cost of upgrading their lighting systems while also lowering their long-term energy expenses.
Warehouse lighting expenses are influenced by a variety of factors, from energy consumption to maintenance and environmental considerations. By implementing cost-saving strategies, such as switching to energy-efficient lighting and utilizing natural light, businesses can reduce their overall lighting expenses while also benefiting from long-term savings and improved sustainability.
Effective management of warehouse lighting expenses requires careful consideration of several factors, from energy consumption and lighting design to maintenance and regulatory compliance. By transitioning to energy-efficient systems such as LEDs, utilizing smart lighting controls, and taking advantage of natural light, businesses can reduce both operational costs and environmental impact. Regular maintenance and proactive planning further contribute to minimizing unnecessary expenses, while also ensuring a safe and productive work environment. Incorporating these strategies into warehouse operations not only reduces energy consumption but also supports long-term sustainability goals and compliance with evolving regulatory standards. As lighting technology continues to advance, staying informed and adaptable will help warehouse managers optimize their lighting systems for ongoing cost savings and efficiency.