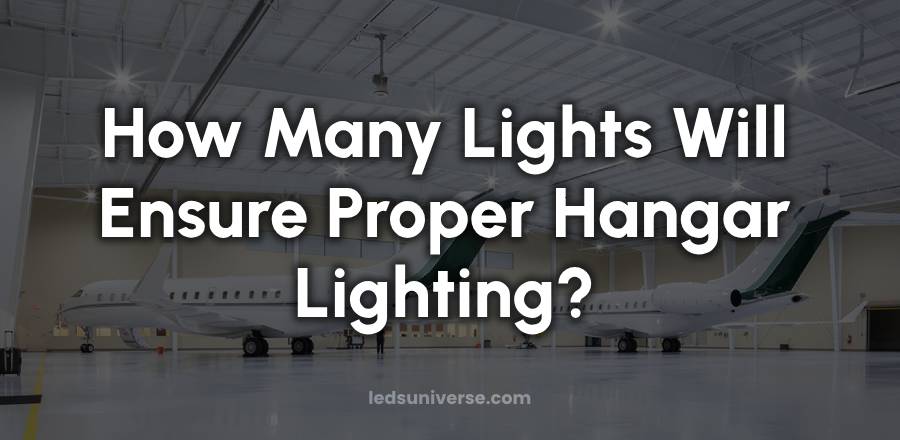
Hangar lighting systems are designed for efficiency, visibility, and adaptability. Carefully calibrated lux levels ensure uniform illumination, while optimized color temperatures enhance clarity for maintenance and inspections. Advanced LED technology and automated controls adjust lighting based on real-time conditions, improving energy efficiency and reducing costs. Integrated safety lighting and smart monitoring systems enhance reliability, ensuring seamless operations. With a balance of precision, technology, and sustainability, modern hangar lighting creates an environment that supports productivity and operational stability.
Modern hangar facilities rely on a blend of design principles, technology, and scientific measurement to create environments that support routine operations, aircraft maintenance, and secure handling of equipment. The design of lighting systems in such facilities has evolved over decades and now follows precise guidelines derived from technical research and operational experience. The thoughtful arrangement of lighting fixtures contributes to effective operational performance and supports a visually comfortable work environment across vast spaces.
Reach out for free lighting consultation
Table of Contents
ToggleIllumination levels, measured in lux, serve as a guiding parameter for configuring lighting systems within hangar spaces. Calculations of lux values are based on operational tasks, spatial dimensions, and the layout of equipment. Measurements commonly range from approximately 300 lux in areas used for general maintenance to 500 lux in zones designated for inspection work. Variations in ambient light, reflective surfaces, and ceiling height lead designers to adjust these values to suit particular locations within a hangar. Designers assess both the uniformity and distribution of light to avoid pockets of excessive brightness or shadowed regions, ensuring that each section of the hangar receives a consistent light output.
Lux, which represents the density of luminous flux on a surface, is the standard unit used to assess the performance of lighting systems. Within hangar environments, thorough measurement techniques are employed. Measurements are taken at several points across a workspace to calculate an average illumination level, ensuring that the distribution is even. In many instances, lux levels are maintained within a variance of 20 percent across an area that can span up to 1500 square meters. This approach minimizes the appearance of glare or dark spots that may affect the workflow. For example, when an area is designed to achieve 300 lux uniformly, designers may use a series of luminaire placements that emit around 8000 lumens each to cover extensive floor spaces effectively.
Different operations within a hangar may require varied illumination levels. Workstations dedicated to detailed inspection might operate with lux values approaching 500, while areas allocated for routine aircraft parking or general storage maintain levels near 300 lux. Designers often incorporate lighting control systems that adjust lux output based on the specific task being performed. An example includes a system that automatically reduces its output by roughly 20 percent during periods of high ambient natural light, while ensuring that the floor maintains over 250 lux during low-light conditions. Such adaptive measures not only support task performance but also help maintain uniformity in visual perception across the entire facility.
The design of hangar lighting systems contributes to the operational stability and overall safety of the environment by assisting personnel in monitoring aircraft, equipment, and the facility layout. The arrangement and performance of lighting fixtures are planned according to established guidelines that address spatial safety and minimize hazards. Overhead lighting combined with supplemental task lighting ensures that all operational areas are uniformly lit, reducing risks associated with uneven illumination. Backup systems are integrated into many designs to maintain visibility during temporary power fluctuations.
Multiple layers of lighting are arranged to provide a consistent environment across all zones within a hangar. Overhead fixtures typically form the primary source of illumination, supplemented by task lighting near workstations where intricate tasks are performed. The coordination between different sources minimizes the occurrence of shadows and glare, which can otherwise affect visual performance. Factors such as the spatial layout, ceiling height, and reflective properties of the surfaces play a role in determining the placement and output of lighting fixtures. In expansive hangars, systems may deploy up to 50 luminaires, each contributing a high lumen output to ensure that even remote corners are well lit. The combined effect of these measures results in a work environment that supports continuous operations while maintaining consistent illumination levels.
Backup lighting systems are incorporated into the design to provide uninterrupted illumination in case of power interruptions or fluctuations. In many hangar facilities, emergency lighting is configured to deliver at least 200 lux across critical areas, ensuring that operations continue seamlessly during unexpected events. Such systems typically involve battery-powered fixtures or units connected to backup generators. When a power outage occurs, sensors trigger these systems to provide immediate illumination, often within seconds, thereby preventing temporary dark spots. A backup system might include a battery bank with a capacity of around 20 kWh, which can sustain a facility of 1000 square meters for over one hour. The seamless transition between standard and emergency lighting helps maintain a stable environment during unforeseen interruptions.
Color temperature, expressed in Kelvin (K), affects how colors are perceived and influences the visual performance of personnel. The range of color temperatures used in hangar lighting is selected to provide clarity and visual comfort while minimizing eye strain. For instance, work areas typically employ lighting within a range of 4000K to 5000K. This range produces a balanced white light that supports detailed visual tasks such as inspection and maintenance. Some modern lighting systems include adjustable color temperature settings, allowing the environment to be modified in real time to suit the task at hand. Adjustable fixtures have settings that can shift from 3500K to 5500K, enabling designers to fine-tune the environment for optimum visual performance.
The color temperature of lighting directly affects the appearance of colors and the clarity of visual tasks. Lower Kelvin values result in warmer hues that may lend a relaxed atmosphere, while higher values produce cooler tones that enhance contrast and focus. In hangar environments where precise visual inspection is often required, a cooler light source—typically around 5000K—is favored to help highlight subtle variations and details. Conversely, areas where broader tasks occur may use a moderately warm temperature, such as 4000K, to balance visual comfort with clarity. The deliberate selection of color temperature supports the visual acuity needed for tasks ranging from routine maintenance to detailed diagnostic procedures.
Designers often adopt specific guidelines that outline the use of color temperature for various zones within a hangar. Zones dedicated to maintenance and inspection are frequently lit with cooler tones around 5000K to enhance the ability to detect minute differences on surfaces or components. Other zones, such as general workspaces or storage areas, might operate comfortably within the 4000K range. The flexibility of modern LED fixtures allows for the adjustment of color temperature in real time. Such flexibility provides an adaptive lighting environment that can be tuned in increments as small as 100K. This precision helps maintain a visually uniform atmosphere and supports the diverse operational demands of a hangar.
Technical assessments conducted over extended periods have observed that environments lit within the cooler spectrum exhibit enhanced visual clarity and reduced instances of color distortion. Systems that incorporate feedback from ambient light sensors adjust the light output continuously, thereby maintaining a uniform Kelvin level throughout the day. This automated process helps accommodate shifts in natural light and ensures that the selected color temperature remains consistent, regardless of external conditions.
In addition to visual clarity, color temperature plays a role in the overall ambiance of the hangar. Modern lighting systems are engineered to counteract potential color shifts that may occur with prolonged use. LED fixtures, in particular, are designed with technology that minimizes spectral drift, preserving the intended color output over extensive operational hours. This stability in color temperature ensures that visual tasks are not affected by gradual changes in the lighting environment, thus supporting sustained operational performance.
Emerging technologies have reshaped the landscape of hangar lighting design. Automated controls, sensor integrations, and energy-efficient LED solutions have collectively transformed how lighting systems are engineered and operated. Contemporary systems integrate digital controls that adjust both lux levels and color temperature based on real-time feedback from the environment. These systems have the capability to adapt illumination from 200 lux to 600 lux in response to changes in ambient conditions, offering a refined approach to operational lighting management.
Advanced hangar lighting systems incorporate automated digital controls that monitor various parameters such as ambient light levels and temperature fluctuations. Sensors positioned throughout the hangar gather data continuously and relay it to a central control unit. The system then automatically adjusts the output of LED fixtures to meet predetermined lux values and color temperature ranges. This technology ensures that any reduction in natural light is compensated for by an increase in artificial illumination, and vice versa, with adjustments that can occur in increments as small as 10 lux. Such precise control provides a responsive environment where the lighting remains consistent throughout different operational periods.
Advances in LED technology have brought about significant improvements in energy efficiency. Modern fixtures consume far less power than traditional lighting while delivering comparable or higher levels of illumination. For instance, LED systems installed in a hangar spanning 2000 square meters may operate at around 15 watts per fixture while emitting approximately 8000 lumens each. These figures translate into substantial energy savings, sometimes exceeding 50 percent when compared to older lighting systems. The use of energy-efficient lighting not only reduces operational costs but also contributes to an environmentally conscious facility design.
Energy management software has further refined the operation of hangar lighting systems. This software monitors performance and adjusts lighting outputs based on real-time data regarding occupancy and ambient conditions. Over time, such dynamic adjustments have resulted in lower overall energy consumption while preserving a stable operational environment. The long operational lifespan of LED fixtures—often exceeding 50,000 hours—ensures consistent performance over extended periods, reducing the frequency of maintenance interventions and contributing to a more stable operational environment.
The selection and configuration of lighting systems in hangar facilities also take into account factors that affect energy consumption and environmental impact. The use of energy-efficient technology such as LED fixtures, paired with automated control systems, has led to reductions in energy use by as much as 60 percent compared to older lighting technologies. This reduction supports the broader aim of lowering the environmental footprint of hangar operations while still providing a high-performance illumination environment.
Maintenance strategies for hangar lighting involve regular inspections and system diagnostics. Modern systems often feature integrated sensors that detect when a luminaire is underperforming or has ceased functioning. Remote monitoring through centralized control panels allows maintenance teams to diagnose and address issues without immediate physical intervention. Typically, inspections are conducted every three to six months. During these intervals, technical teams review the performance of LED fixtures, sensor functionality, and overall light uniformity across the facility. The use of automated diagnostic tools supports prompt identification of discrepancies, which helps maintain operational stability throughout the facility.
Over time, automated maintenance systems have been shown to reduce response times and extend the lifespan of lighting installations. Data collected from long-term monitoring indicates that when sensor systems detect anomalies, they can trigger corrective actions before human intervention is required. This integration of smart diagnostics into the lighting system supports efficient upkeep and contributes to the overall smooth operation of the facility.
Hangar lighting design incorporates multiple layers of planning, measurement, and technology to support a stable and visually coherent environment. The detailed assessment of lux levels, arrangement of fixtures, and control of color temperature collaborate to form a lighting solution that meets the operational demands of aircraft maintenance and storage facilities. Automated controls, sensor feedback, and energy-efficient designs provide a responsive system that adjusts to environmental changes and operational conditions.
The combined approach of detailed lux management, safety-focused design, and adaptive color temperature controls results in a lighting system that supports a visually consistent work environment. Modern technologies allow for precise adjustments and automated monitoring, ensuring that the environment remains stable during routine and emergency situations alike.